3 Elements of Just In Time
The 3 major elements of Just In Time or JIT are
- Smaller Inventories
- Shorter Lead times
- High quality processes
Just In Time (JIT) is a business philosophy that centers around the idea of cost reduction, minimization of waste and improved operational efficiency. A wide variety of industries generally apply this system to inventory, production and other operational aspects of businesses. The core idea behind JIT is to make only what is needed, when it is needed, and in the exact amount needed. By doing so, the organisation can minimise resources and improve quality. There are three main elements of JIT: smaller inventories, shorter lead times, and high quality processes.
First Element of Just In Time: Smaller Inventories
Smaller inventories are an integral part of a JIT system. Reducing the amount of inventory on hand allows resources to be conserved and costs to be cut. The goal of JIT is for businesses to only have enough inventory to keep up with actual customer demand. This helps them avoid overextending or overproducing and eliminate the need for costly storage. To achieve this, businesses must track the amount of inventory needed. Additionally, they must also adjust their production process to meet the needs of customers.
Second Element of Just In Time: Shorter Lead Times
Shorter lead times is another element of JIT system. This helps businesses reduce costs and save resources by ensuring everything is completed quickly and efficiently. By reducing time between ordering materials and when production starts, businesses can avoid long queues and delays that increase costs. For this element to be effective, businesses must have strong communication between departments, clear goals and objectives, and the resources necessary to complete tasks quickly.
Third Element of Just In Time: High quality processes
Finally, the third element of JIT is the use of high quality processes. The goal of JIT is to reduce costs and waste while improving efficiency, and one of the main ways this can be achieved is by reducing errors and rework. To do this, businesses must define their processes and procedures as clearly as possible and must consistently monitor and review them to make sure they remain effective. Additionally, businesses must ensure they have adequate quality control measures in place to identify any potential issues and address them promptly.
Just In Time is a business philosophy that is designed to reduce costs, minimise waste and improve operational efficiency. This can be achieved through the use of three key elements: smaller inventories, shorter lead times, and high quality processes. Businesses must utilise these three elements of just in time to become more effective, cost efficient and have an overall better operational performance.
Master Lean and Six Sigma Acronyms in No Time!
The Ultimate Guide to LSS Lingo – Yours for Free
Subscribe and Get Your Hands on the Most Comprehensive List of 220+ LSS Acronyms Available. No more searching for definitions, no more confusion. Just pure expertise at your fingertips. Get your free guide and other ebooks and templates today. Download Now!
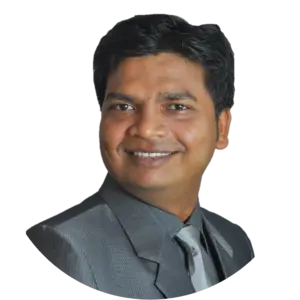
Sachin Naik
Passionate about improving processes and systems | Lean Six Sigma practitioner, trainer and coach for 14+ years consulting giant corporations and fortune 500 companies on Operational Excellence | Start-up enthusiast | Change Management and Design Thinking student | Love to ride and drive
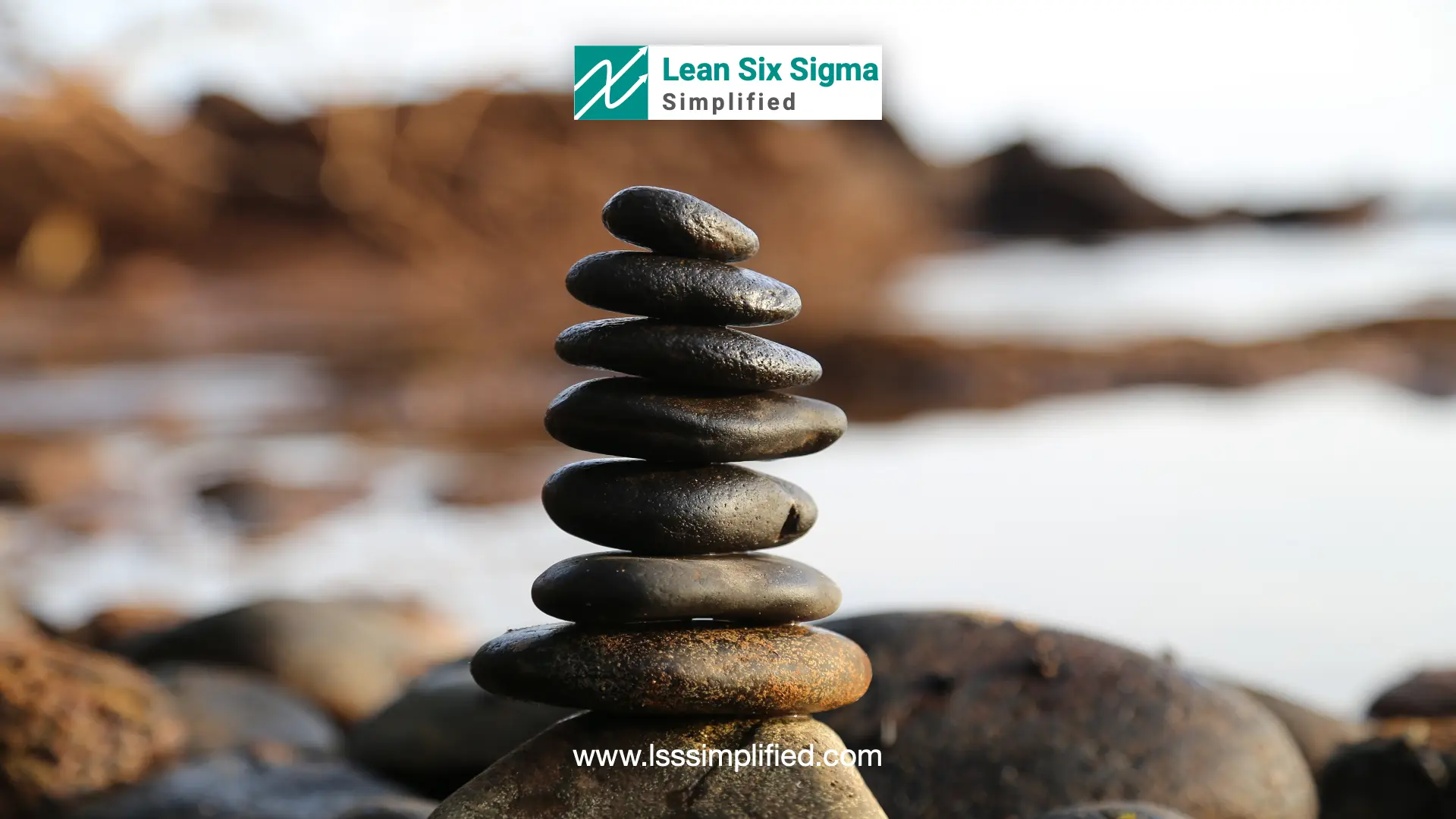
7 Principles of Lean
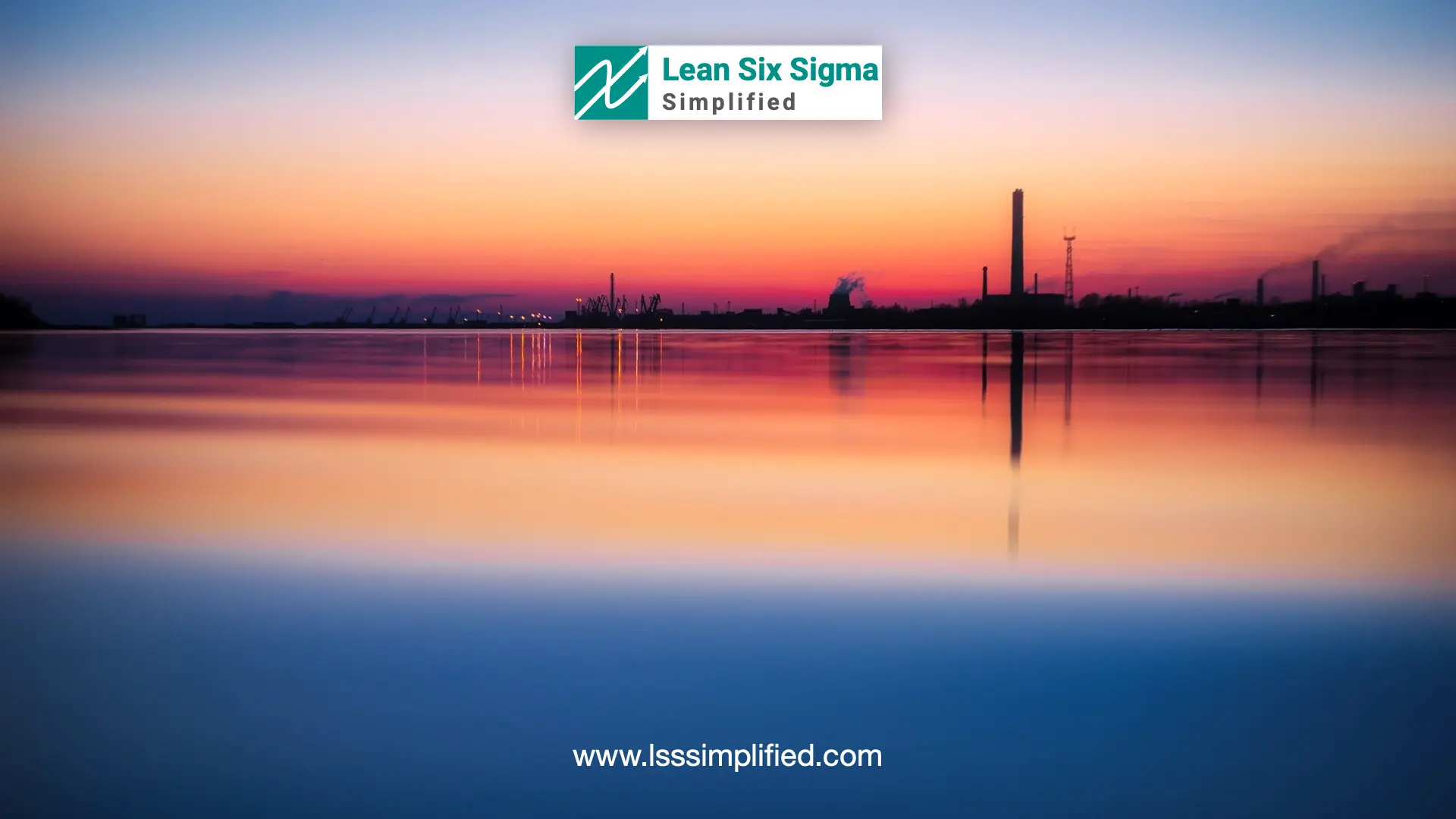
Origin of Lean

Next generation Lean Six Sigma – Harnessing the Power of AI

What is Lean Six Sigma and how it helps your career
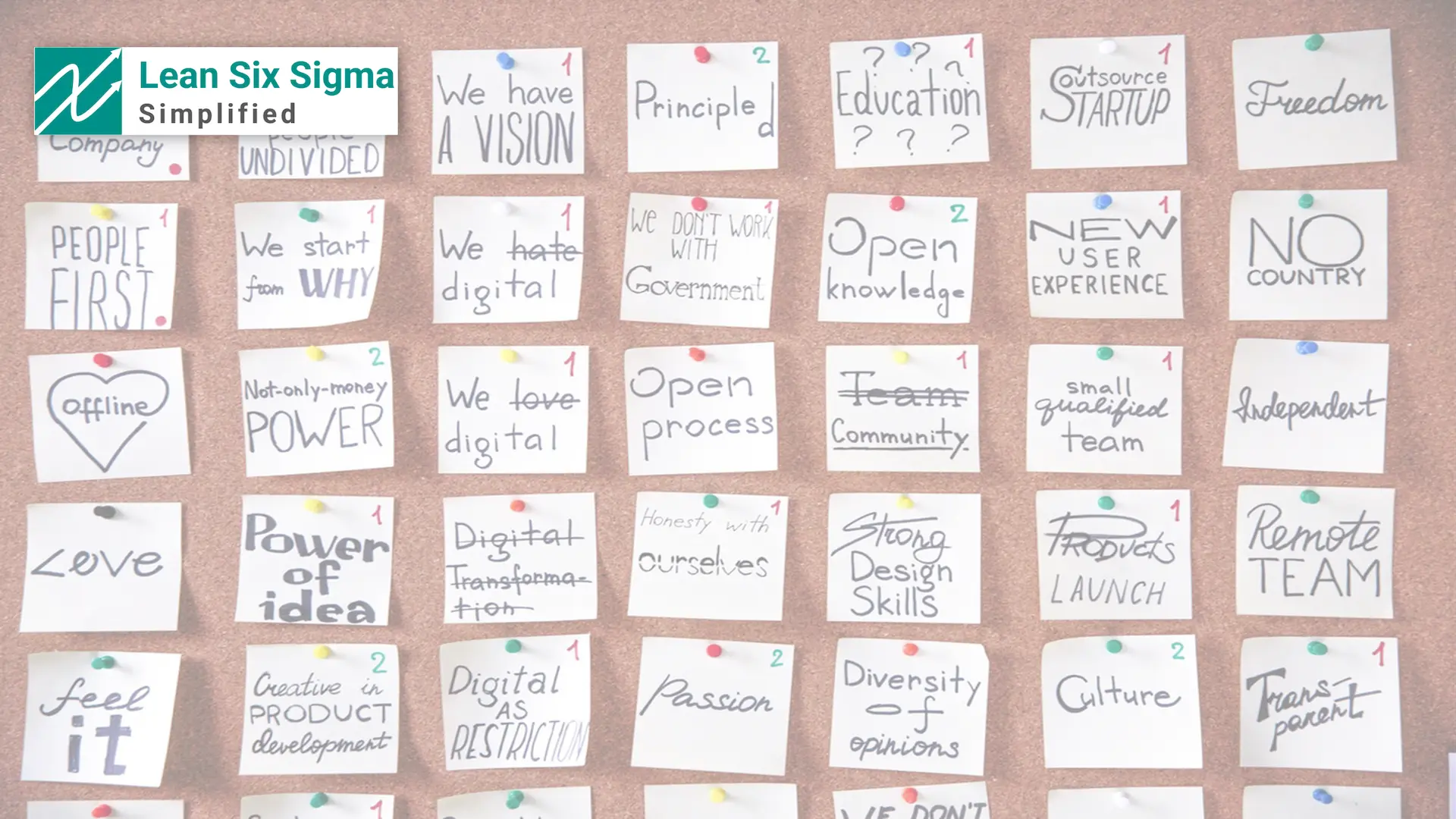
Nominal Group Technique Definition, Examples Steps
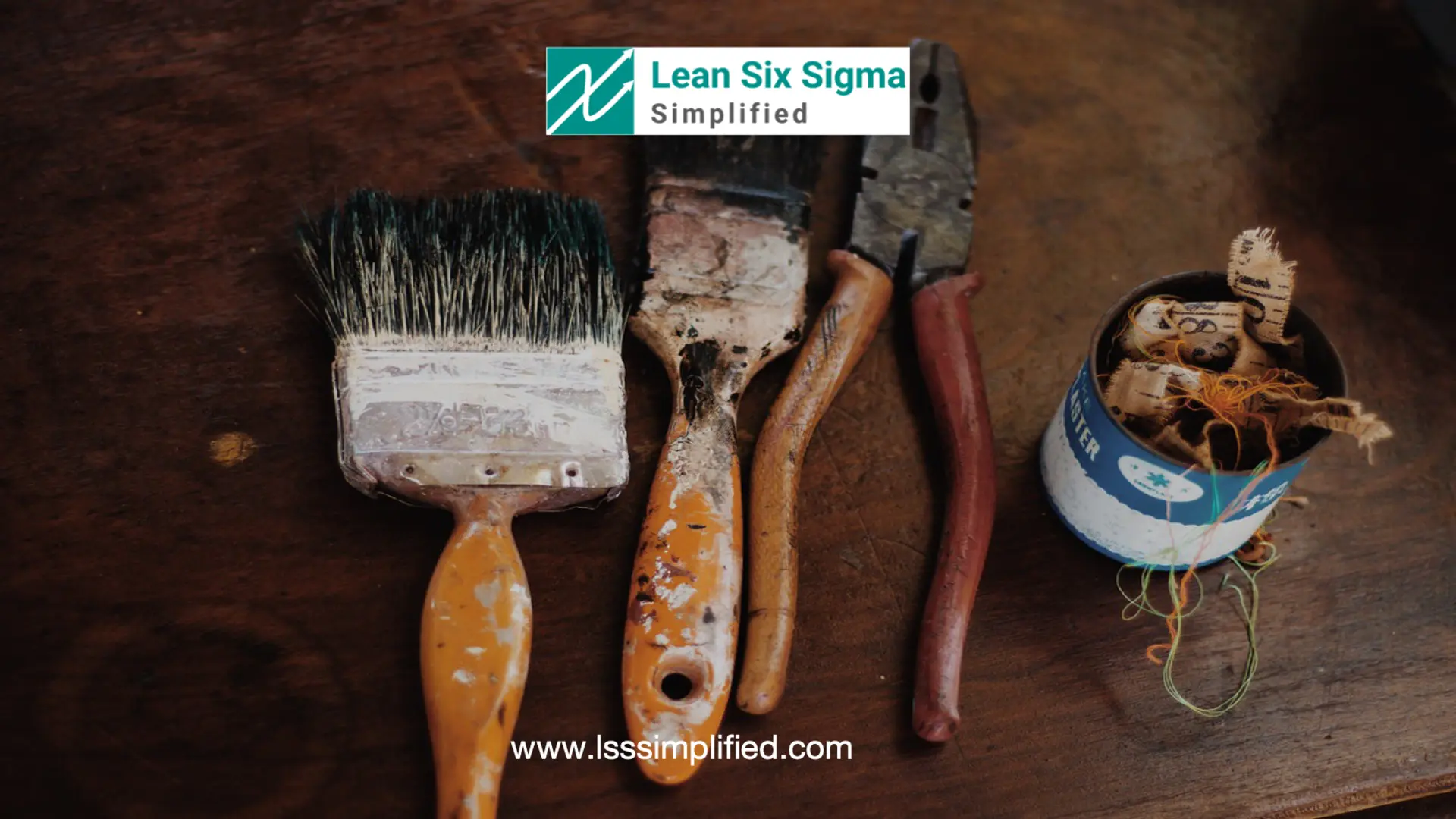
What are the measures of Variation

What are the measures of Central Tendency
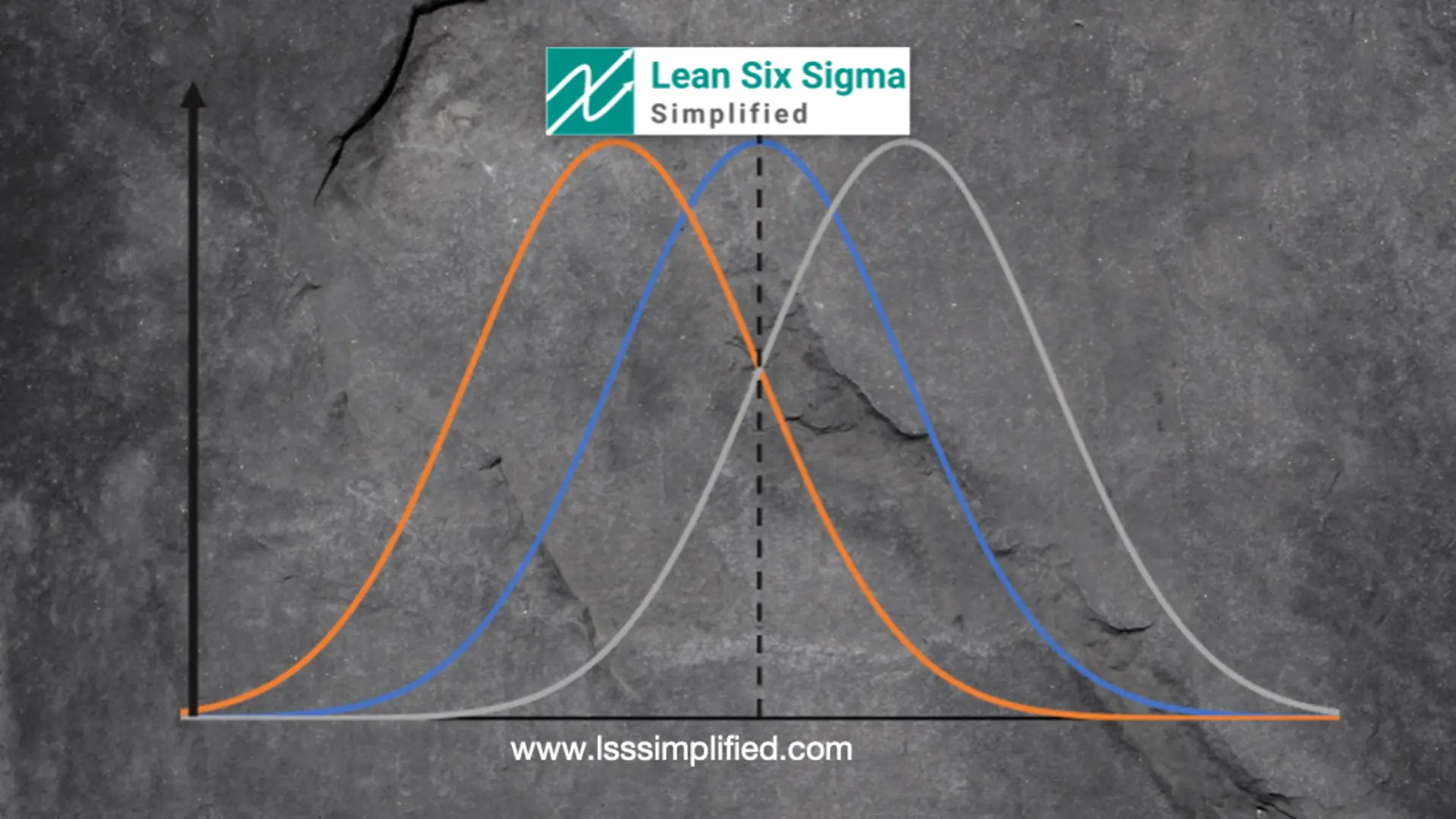
Normal Distribution for Lean Six Sigma

Probability Distribution for Lean Six Sigma
